生産性を上げたい
生産性を上げることは物流担当者の大きなテーマです。複数の物流センターを持つ企業はこの数値で各センターを評価したりします。ここでは、まず生産性管理とは?から始め実際の改善手法について述べさせて頂きます。
生産性管理とは
生産性向上を図るにはまず生産性管理を行うことから始まります。
数値で現状把握=>改善策実施=>結果の数値管理 この繰り返しです。
人時生産性( /MH)
生産性を表す単位として、/MHという単位をよく使います。Mは人でHは時間です。つまり1人1時間どれだけどのくらいの作業(処理)ができるかという単位になります。
物流現場では常日頃からの調査により、各作業の/MHを把握しておく必要あります。この1人1時間当たりの処理量を把握しておくと、その値を基に作業計画(作業人員や作業時間)の組立てができます。
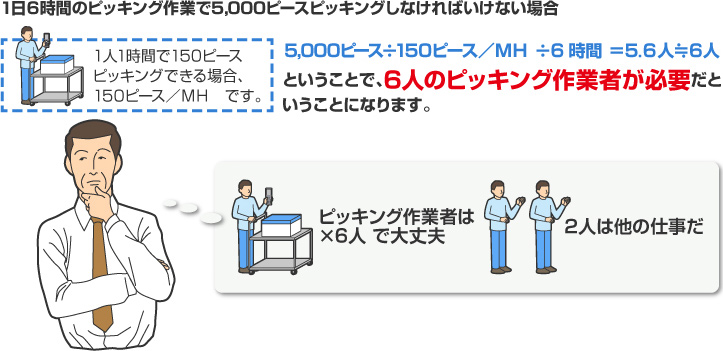
個人生産性( /MH)
生産性向上には作業者の管理が不可欠です。物流現場での作業においては当然個人差があります。動きの速い人、速いが間違いの多い人、作業は正確だが遅い人、さぼる人、様々です。ミスの多い人は徹底教育する、適材適所の人員配置をする、賃金差を付ける、などの作業者別対応策と現場確認が必要です。
ハンディターミナル等を使用してのピッキング作業においては、個人生産性データを容易に取得することができます。誰が何時から何時の間にどれだけの作業をしたかのデータです。
目標値設定
生産性(/MH)を管理できたら、個人生産性データより生産性の目標値を設定します。この値を基に、本日の物量や件数、作業人数、目標作業終了時間 をホワイトボードなどを使って作業者にハッキリと提示します。これは、作業者の意識向上を図るのと同時に、帳尻合わせの作業(件数の多い少ないに関わらす終了時間は一緒)を防ぐことになります。
生産性の目標値だけでなく精度の目標値も設定しないと作業が乱雑になる可能性あります。
ハンディターミナル等を使用してのピッキング作業においては、1件のピッキングが終了したタイミングでハンディ画面に生産性を表示して作業者にアナウンスすることができます。
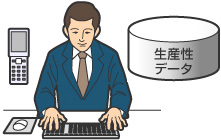
滞留とボトルネックを探せ
生産性を上げようとする場合、時間短縮やスピードアップということを考えますが、見落としがちなのは、作業をしていない時間がどれくらいあるかです。この空き時間は時間の無駄だけでなく、作業のリズムも狂わせ、集中力を無くし作業精度を落とす要因でもあります。物流作業というのは流れ作業や巡回作業が主ですので滞留などから待ち・空き時間がよく発生します。
図1
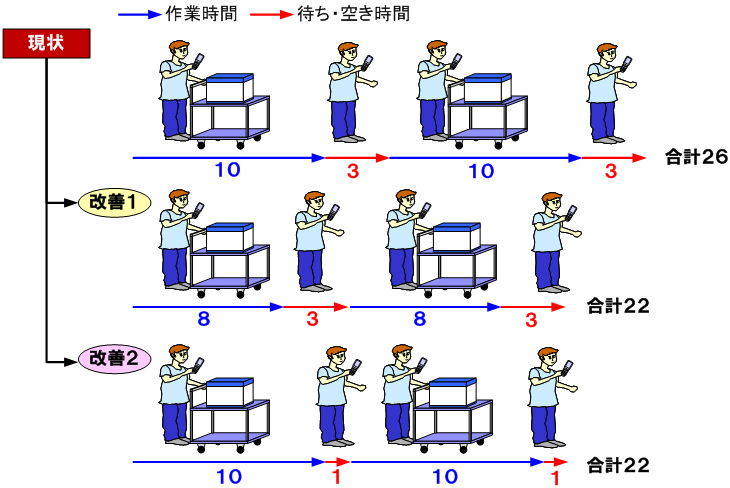
改善1は作業時間を短縮する方法です。改善2は待ち・空き時間を短縮する方法で、すなわち滞留が発生している原因を突き止め、対策を取ることです。
改善1、2の両方とも重要ですが、物流責任者としては改善2に目を向けるべきです。何故なら、運用ルールや今までの慣習が滞留を発生させている要因になっていたりするからです。
改善2の滞留要因突き止めは、慣習から物流担当者には見えにくいものになっていることが多いです。第三者に現場を見てもらったりして指摘を受けた方がいいのかもしれません。
待ち・空き時間短縮の参考例
以下のグラフは図1の出荷データを実際ピッキングする順番に店舗の並びを変えたグラフになります。赤線が店舗毎の出荷物量で青線が店舗毎の出荷アイテム数です。左から右への順番でピッキングします。
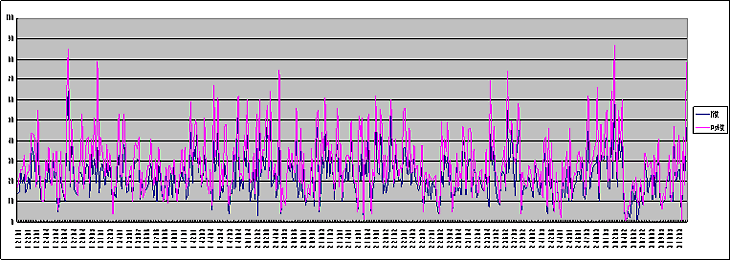
物量の較差が大きいので、通路幅が狭く追い越ししづらい場合は必ず滞留してしまいます。これでは作業していない時間が発生して、結果的に生産性を落としてしまいます。
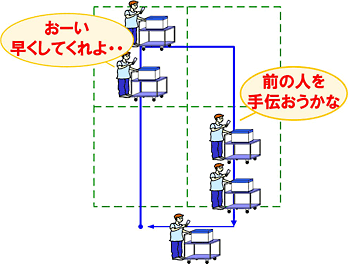
同一のデータを出荷物量の少ない順に並べなおすと下のグラフになります。
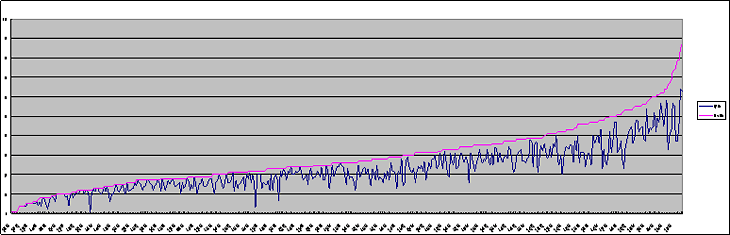
物量がなめらかに増えていきます。この順番でピッキングを行えばほとんど滞留することなくピッキング作業を行えます。
しかし、出荷順とは違う順番でピッキングされるので、その後の荷揃え作業が大変になります。こちらの物流センターにはソーター(自動仕分けコンベヤ)が導入されており、荷揃え作業が自動化されてました。だから可能だったということになります。
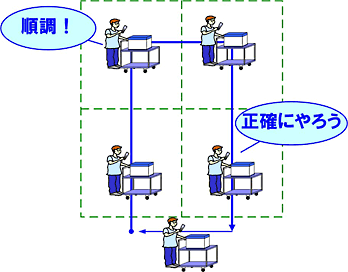
PDCAサイクル
図1の2つの改善方法に共通していることはPDCAサイクルの実行です。

但し、そんなにうまくいくことは滅多にありません。改善策を模索した時点で大きな壁にぶつかります。限られたスペースであり、得意先様へのサービスであり、社内調整かもしれません。しかし、それを解決していくのが物流担当者の仕事でしょう。粘りと根気が大切です。
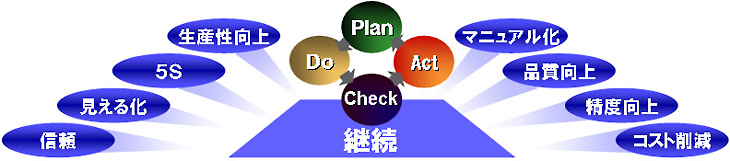
PDCA(Plan=>Do=>Check=>Act)を繰り返すことが重要です。更に重要なのはそれを継続・引継ぎすることにより、会社としての実力を蓄えていくことです。