物流コスト削減
物流コスト削減というのは物流責任者であれば最大のテーマであり、最大の任務でもあります。物流コストとは一般的に配送費,保管費(倉庫含む),人件費,物流設備費,情報システム費,ランニングコスト,事務所費などからなるトータル的な費用のことを差します。
物流コスト削減としては、
- 物流拠点統廃合、製造や営業部署も絡めての在庫削減、3PLへの外部委託、などの全体最適やSCMの観点からの物流コスト削減。
- 庫内の保管費,人件費,設備費,ランニング費など改善や投資コスト低減からの物流コスト削減。
の大きく2パターンがあると言えます。
- は当然、大幅な物流コスト削減をもたらす可能性が有り、会社上層部や物流責任者は当然検討すべきことです。
- は大幅な物流コスト削減をもたらす可能性は低いのですが、改善活動やPDCAを地道にかつ柔軟に繰り返すことにより、改善意識と物流コス トへの意識が高まり、会社としての物流設計力や提案力がアップするでしょう。
今回はほとんどの物流関係者に共通する2)の物流コスト削減について掲載致します。
物流コスト削減は5S、見える化、ルール化から
私どもがまず倉庫内を見学して着目するのは、5S(整理、整頓、清掃、清潔、躾)と見える化ができているかどうかです。倉庫内を見て回ると下記のようなことが必然的に目に入ってきます。
- 各作業エリアや保管エリアの区分けの明確化
・保管エリア ・通路エリア ・備品置場所 ・ゴミ箱
・不要資材置場 - ロケーションや商品配置の明確
・ロケ-ションサイン ・棚札 ・エリア名称 - 5Sとあいさつ
・清掃、整理整頓 ・備品置場所の固定化
・あいさつ ・朝礼昼礼 - ホワイトボード活用
・人員配置 ・本日の入出荷物量やアイテム数
・昨日の結果・目標値設定(終了時間,生産性,精度) - 作業手順の見える化
・作業マニュアル ・基本ピッキング動線矢印
・禁止,注意事項 ・危険区域
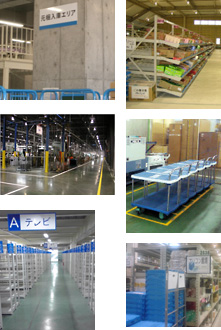
何故必要なの
これらは物流コスト削減には一見関係無さそうな感じがしますが、これらができているかどうかは物流コスト削減に向けての体制として大きな差があります。何故なら5Sや見える化やルール作りというのは物流コスト削減の土台のようなものだからです。
倉庫内の作業はマニュアルとルールを作り、それを徹底して継続実行していくことを基本としてます。これは簡単なようでそう ではありません。マニュアル作りや教育そのものも大変ですが、作業者も替わりますし、また得意先からの納品要件が変わる場合もあります。それに対してこのマニュアル&ルールを柔軟に変えていかなければなりません。5Sや見える化は庫内の最低限かつ基本的なルールと言えます。これが出来てなければコスト削減に繋がるような改善・改革はできません。
しかし、これらのことを継続維持していけば生産性や精度が維持できるということです。また、物流コスト削減への取組みや新規業務への対応等の際にも必ず活きてきます。
ルール無しの倉庫では
逆に、5Sや見える化ができてない倉庫は、商品が乱雑に並び積み上げられていたりで、その場しのぎの商品保管になってるというのがよくあります。作業エリアについても何がどうなっているのかさっぱりわかりません。質問すると現場担当者のみが理解しているというのがよくあるパターンです。現場担当者のやり方がルールそのものということです。
このような倉庫では改善点が比較的簡単に見つかります。保管方法や作業等について、根拠無くやっていることが多いので、第3者が効率性の観点から現場を見ると疑問点や改善点が次々と見えてくるのです。
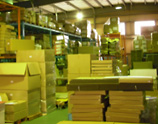
物流コスト削減は意識改革から
5S、見える化、ルール化というのができているかそうでないかの差は倉庫内の各メンバーに改善意識が有るか無いかだと思います。個々の改善意識が結集されれば、必然的に実現されていくでしょう。
物流機器導入と費用対効果
私どもがお客様からよく相談を受けるのは、「○○○を導入して人を減らしたいのだが提案してくれないか。」という相談です。
※○○○はマテハン機器や物流システム
物流システムや自動化機器を導入すれば人員削減することができます(使い物にならなかった例を見たこと有りますが)。
そこで必ず費用対効果がどうなのか?ということが課題となってきます。私どもがお客様に提案する場合も、それを避けては通れません。
費用対効果とは、正式な意味とは違うかもしれませんが、一般的に機器やシステムを導入してどれだけ物流コスト削減できるかということになります。いわゆる導入前と導入後のコスト比較です。
導入前と導入後のコスト比較
下図はリストでの手仕分け作業とソーター(自動仕分け機)を導入した場合のコスト比較項目例になります。
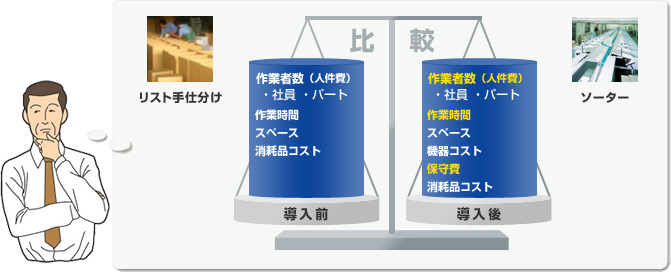
導入後の費用が安ければ導入価値があるということになります。
この比較項目の中で導入後の作業者数と作業時間をどう見るかが大きなポイントです。
当然、機器導入前ですから推測値になります。この推測値は上図の天秤の傾きに大きく影響しますので、しっかり実作業を想定して算出する必要あります。シミュレ-ションソフトを活用するのも一つの手ですが、各作業にかかる時間は同様に推測値を設定することになります。
見逃しやすいのはメインとなる作業の前後の作業です。
ソーターであれば商品投入人数や仕分け後の商品箱詰め人数は当然割り出しますが、商品を投入ステーションに供給する作業や満杯になった箱の排出や搬送作業など見落としがちです。発生する全ての作業を洗い出してその人数(工数)を算出する必要があります。
また、マテハン機器メーカーの営業マンを信用し過ぎないことです。
どうしても自社製機器を販売しなければならないので、機器能力や導入効果を大げさに言いがちです。
保守費・維持費
注意すべきは保守費です。物流機器の導入経験が無い会社はこの保守費の存在を見落としがちです。機械は壊れるものなので費用がかかるのはわかってますが、この費用がどのくらいかはまったく想定できないでしょう。
マテハン機器メーカーは営業部隊とサービス部隊が別会社になってたりしますので、導入時に保守費用がどのくらいかかるのか自ら言ってくる営業マンはほとんどいません。しっかり確認しておくべきです。
大型機器のハードに関しては定期点検が必要になります。ソーター等の機器になりますと、一般的に年2回ぐらいの定期点検を行います。機器ダウンしてからのメンテナンスですと業務がストップしてしまいますので、壊れる前に点検にて部品を交換するという考えです。当然、年数が経てば経つほど交換部品も多くなりますので、保守費用がアップしていきます。
コストで表現されない付加価値
こうやって導入前と導入後のコスト比較をすると、不思議なことにとんとんの場合がよくあります。私どもとしては導入後の方が安ければお客様に提案しやすいのですが、うまくいかないものです。物流機器がそういう価格設定されているとは思えませんが。
こうなると、会社としてこの投資は見送り、という判断になる場合がほとんどです。費用対効果が充分でないということなので当然そうなるでしょう。
しかし、本当に導入価値は無いのでしょうか。機器やシステムを導入した場合に付加価値として以下の様な導入効果が生まれます。
- 作業精度向上
- 精度向上による在庫誤差削減
- 信頼性アップ
- 熟練者不要
- 教育時間短縮
- 作業計画の立てやすさ
- 実績,進捗,生産性のデータ管理
これらはコストで表現がするのは難しいのですが、重要な導入効果であり、最終的にはコストダウンや得意先の信頼度アップにも繋がる要素です。コスト比較も重要ですが、この付加価値追求をおろそかにすると、サービスレベルが低下して競合会社にも差を付けられてしまいます。仮にソーター導入ではコスト削減にならないのであれば、安価なデジタルアソート(DAS)やハンディターミナル仕分け等の方法も検討して上記の導入効果を生み出す手段を模索すべきだと思います。
機器&システム導入について
物流機器&システムは導入は物流コスト削減だけでなく、いろんな付加価値や相乗効果が現れることが多く、導入した方がいいというのが私どもの基本的な考えです。しかし、高価な物流機器を次々に導入して負の遺産を抱えてしまっている企業もありますし、荷主との契約が切れて物流機器のみが残ってしまった企業もあります。費用対効果、付加価値、機器やシステムの柔軟性、保守費用、自社の企業文化、などから機器選択・導入されるのがいいかと思います。
人件費削減のためのライン生産方式とセル生産方式の比較
物流コスト削減という意味で人件費の削減(作業者数や作業時間削減)は大きなテーマです。人1人削減するのに相当の工夫と努力が必要です。但し、物量に応じて作業者数を調整する(例えば曜日に応じて作業者数を変える)ということを実行されている倉庫は多いと思います。物量の曜日変動や月変動だけでなく、2~3年後の物量増減など、変化が読めない時代になってますので、物流業務の組立ても変化に対応しやすいやり方にして、作業者数の増減で適正な物流コストを維持することが重要です。
そこで重要なのは作業の組立て方です。ここ数年前から製造現場(特に組立て工程)でセル生産方式が取り入れられてます。
この考え方は、物流にも当てはまりますので、人件費削減という観点からライン生産方式とセル生産方式の比較を行ってみます。
※ライン生産方式とセル生産方式の意味についてはウィキペディア等で調べてください。
倉庫内業務は一般的にライン生産方式
倉庫内業務のほとんどはライン生産方式で行われてます。ピッキング、検品、梱包など各作業を行う場所と人を決め、その専任者が自分の受持ち工程を終了したら、次の工程の専任者に渡していくやり方です。物流業務は作業を正確にかつスピーディに行うことを求められるので、必然的に、単純作業の繰返しになるライン生産方式になっていると思われます。しかもこの方式は熟練性を必要としないので、派遣やパート、いろんな能力の人を適材適所に配置して、高い処理量をこなすことができます。
ライン生産方式とセル生産方式の比較
下の図は2つの方式を出荷運用で説明した例です。ライン生産方式の方は各作業を専任化して、担当者はその作業のみを繰り返すやり方です。セル生産方式の方は1人が全ての作業を受持つやり方です。
ライン生産方式の方は各作業のバランスが取れていれば、コンベヤが搬送してくれることもあり、処理能力は高いです。しかし、全ての作業者が常にフル作業している訳ではありません。例えば空コンテナをセットする人は余裕があるでしょうし、それぞれの作業者がその時の作業ボリュームにより待ったり、急いだりすることもあるでしょう。
また、作業者数の増減調整という観点から見るとどうでしょう。各工程の作業内容と作業者数で流れ作業のバランスを取っているので、一つの工程の作業者を削減すると前後の工程に影響が出て、暇な工程と忙しい工程が発生してしまいます。作業者数の調整が難しいということです。
一方セル生産方式の場合は全ての作業工程を1人でやるので常にフル作業です。休んだり、待ちなどが発生する要素がありません。ただ作業者の交錯による時間ロスはあるかもしれません。また、作業者数の増減調整が簡単です。1人減らせばその分の処理量が減るだけで、人時生産性(/MH)は変わりません。
ライン生産方式

作業内容
それぞれの専任者が
- 空コンテナをコンベアにセットする。
- デジタル表示器の指示でピッキングする
- 流れてきたコンテナを梱包作業台で梱包する。コンテナと箱をコンベヤに投入する。
- 空コンテナと商品箱をカゴ車に積む。
- カゴ車が満杯になれば搬送する。
特徴
- 単純・専任作業なので作業習得が簡単。
- 各作業の作業量バランスが崩れると待ちや滞留が発生する。
- 各作業者が常にフル作業してるとは限らない。
- 前後の工程を意識して作業する。
- 一つの工程の作業しかやらなければそれしかできない。
- 作業者数の増減が難しい。
- 適材適所の人員配置が可能である。
セル生産方式
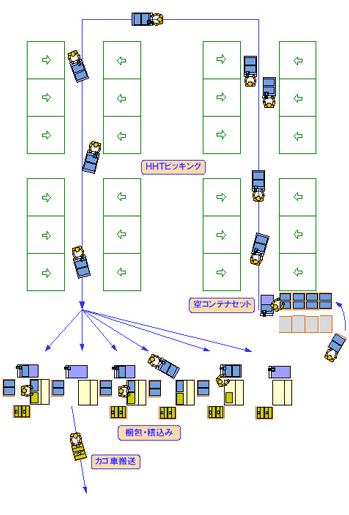
作業内容
1人の作業者が
- 空コンテナを台車に積む。
- 無線ハンディの指示でピッキングする。
- 空いている梱包作業台で梱包する。
- 空コンテナと商品箱をカゴ車に積む。
- カゴ車が満杯になれば搬送する。
特徴
- ある程度の熟練・作業習得が必要。
- 待ちや滞留は基本的に発生しない。
- 各作業者が常にフル作業。
- マイペースの作業になる可能性がある。
- 個人能力がはっきりするので競争意識を持って作業する。
- 作業者数の増減が容易。
作業の組立て
これからは物流もセル生産方式を採用すべきだ、と言っている訳ではありません。但し、作業組立ての中でライン生産的な組立てをするか、セル生産的な組立てをするか、あるいは両方の方式を組み入れるかは、大きな設計ポイントと言えます。それぞれの倉庫で様々な条件と考え方が違います。両方の方式に着目して、それぞれの良さを組み入れて、柔軟性のある物流設計をすべきだということです。
現場見学例
最近見学した倉庫の例です。
デジタルピッキング、スキャン検品、梱包の3工程のライン生産方式でした。稼働後、検品と梱包のスピードが合わずに梱包待ちの箱が滞留してしまうので、コンベヤによるループ(バッファ)ラインを新たに作り、箱が滞留しても問題無いように改善したとのことでした。溜りすぎると検品者が梱包作業にまわるのです。ループラインの駆動コンベヤはかなり長いし、スペースとして30坪ぐらい使ってました。
確かに箱が滞留して溢れる問題は無くなりましたが、これは問題が無くなっただけであり、改善できたとは言えません。
しかも、スペーズやコンベヤ費用に関しての物流コストはアップしたでしょう。