精度を上げたい
物流センター内の業務において精度が落ちると、必ず在庫誤差として表面化します。この在庫誤差は在庫ロスの金額だけでなく、在庫引当処理が狂い、そのため出荷業務にも影響するなど悪循環を生み出します。
精度をあげるには、ハンディターミナルでの検品システムを導入して、各所でスキャン検品するのが、最も効果のでる手段だと思います。
もうひとつは間違えない運用ルールを作り出し、それを徹底することです。それにはマニュアル作成や見える化が必要です。
どのような作業やタイミングでどのようなミスが発生するかと、その解決策をまとめてみました。精度改善の参考になればと思います。
入荷時のミスと解決策
商品違いミス
商品マスタのケース入数と実際入荷されたケース入数が違う。これは小さなメーカーが多い日配品の物流センターで多く見られます。即、仕分けする場合は仕分け時に混乱が発生して入数違いが判明します。在庫品の場合、実在庫バラ数の在庫誤差が発生します。
解決策
ハンディターミナルで入荷検品を行っても、入荷数量は目視確認して手入力するのが一般的ですのでこのミスは発生します。入数を入荷予定リストやハンディターミナル画面に表示して実際の商品入数を徹底チェックする必要あります。現場でチェックできても商品マスタの入数を変更しなければ、次回入荷時に同様のことが発生します。頻繁に発生する場合はハンディターミナルでの入荷検品時に実際の入数を入力して商品マスタ入数を書き換えているセンターもあります。
ケース入数違い
商品マスタのケース入数と実際入荷されたケース入数が違う。これは小さなメーカーが多い日配品の物流センターで多く見られます。即、仕分けする場合は仕分け時に混乱が発生して入数違いが判明します。在庫品の場合、実在庫バラ数の在庫誤差が発生します。
解決策
ハンディターミナルで入荷検品を行っても、入荷数量は目視確認して手入力するのが一般的ですのでこのミスは発生します。入数を入荷予定リストやハンディターミナル画面に表示して実際の商品入数を徹底チェックする必要あります。現場でチェックできても商品マスタの入数を変更しなければ、次回入荷時に同様のことが発生します。頻繁に発生する場合はハンディターミナルでの入荷検品時に実際の入数を入力して商品マスタ入数を書き換えているセンターもあります。
バンド掛けケース品と半裁品
ドライ食品で多く見られますが、小さい2ケースをバンド掛けされて納品される商品があります。入荷検品時にこれを2ケースと見る人と1ケースと見る人がいて、よく間違えられます。
解決策
入荷現場に商品の写真を貼るなどして入荷検品者に徹底させるなどの運用ルールが必要です。ハンディターミナルでの入荷検品では該当アイテムの場合メーセージを出して入荷検品者に注意を促すこともできます。
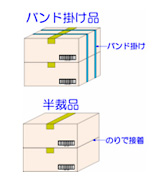
日付・ロット違い
食品、菓子、酒の物流センターでは賞味期限日や製造日のチェック(受入基準日や日付逆転)がほとんどの物流センターで行われてます。これを怠ると出荷に関しても日付逆転や出荷許容日オーバーが発生してクレームや返品の基になります。
解決策
ハンディターミナルでの入荷検品が必須と言えます。ハンディターミナルに日付やロットNOを入力することにより、前回入荷時との日付逆転や受入基準日オーバーをチェックすることができます。
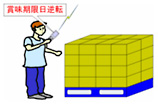
入庫(棚入れ)
間違ったロケーションに棚入れする。ピッキング時に気付かない場合、出荷ミスが発生します。ピッキングをハンディターミナルで全数スキャン検品していればチェックできますが、デジタルピッキングシステムの場合だとピッキングする際に商品名チェックなど行いませんので、気付かずに次々とミスを発生させることになります。
解決策
ハンディターミナルでの棚入れ時に間違いないかチェックすることができます。チェック方法は入庫ラベルのバーコード⇔ロケーションコードのチェック、商品JANコード⇔棚ラベルJANコードが同一かのチェックなどがあります。ハンディターミナル未使用の場合は商品JANコードの下3桁⇔棚ラベルJANコード下3桁を目視でチェックすればミスはほぼ無くなります。
出荷時のミスと解決策
商品違いミス
ハンディターミナルなどでのバーコードスキャン検品を行って無い場合発生します。そもそも棚入れ時に間違っている場合もありますし、ピッキングリストのロケーションや商品名読み間違いなどがあります。
解決策
- ハンディターミナルでのピッキング
ピッキング時に商品バーコードをスキャンしますので商品違いミスは無くなりますが、
・バーコードが付いていない商品は棚ラベルのJANコードをスキャンする。
・JANコード不良の場合は手入力する。
などの商品のJANコードをスキャンしなくてもいい逃げ道を普通作りますので、そこで商品違いミスの可能性が生まれます。
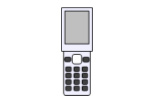
- デジタルピッキング
リストピッキングと比較するとピッキングミスは大幅に削減されます。但し、左右や上下のピッキング間違いが発生しないわけではありません。精度を更に上げるためにデジタル表示器の指示でピッキングしてコンテナに投入する前にDPS連動スキャナーでスキャンしてチェックする方法もあります。
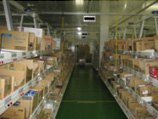
- JANコード下3桁チェック
ピッキングリストにJANコードの下3桁を大きく印字して、商品をピッキングする際に下3桁が商品のJANコードと一致しているかの確認をします。いわゆるハンディターミナルを導入せずに精度を上げる方法です。
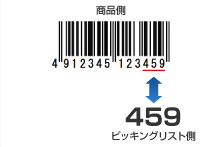
数量ミス
リストピッキングの場合は勿論発生しますが、ハンディターミナルなどでピッキングする場合も数量入力機能を設けると、全品スキャン検品しないので発生します。
解決策
ハンディターミナル等の商品バーコードスキャン検品する場合の数量入力機能は仕方ない商品のみに徹底する。
- 重量検品
計量器付きピッキングカートの場合、ピッキングした商品をカート(台車)上のコンテナに載せると計量して数量をカウントすることにより数量ミスを防ぎます。
間口違いミス
リストピッキングやデジタルピッキングの場合、スキャン検品しなければロケーション間口の上下ミス、左右ミスが発生します。
解決策
- ハンディターミナル等の商品バーコードスキャン検品すれば防止できます。あるいはJANコード下3桁チェックも有効です。
- ロケーション間口の仕切りや上下を明確にすることが重要です。
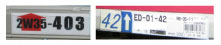
棚札に矢印マークを入れると上下間違いミスが低減します
ロット(ピッキング単位)ミス
ピッキング数量1という指示に対して1バラをピッキングするのか、1ロット(小箱など)をピッキングするのかのミスです。
解決策
事前にロット単位で袋詰めするなどのロット加工作業をしておく必要あります。あるいは商品位置に写真を貼り付けてロット単位を明確にしておくことが重要です。
荷合せミス
複数のエリアでピッキングして、それを荷合わせする場合、違う配送先を荷合わせしたりしてミスが発生します。
解決策
- 各エリアで発生したコンテナ数をデータ管理して、荷合わせ時に個口数をチェックする。
- 各エリアで発生したコンテナ(コンテナラベル)を荷番データ管理して、荷合わせ時にハンディターミナルで荷合わせ検品する。