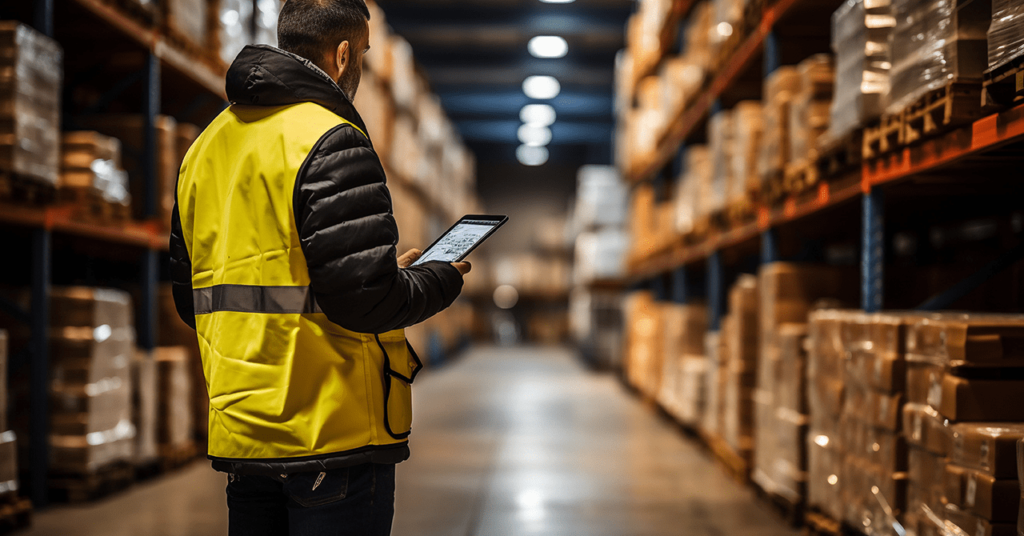
物流倉庫におけるピッキング作業は、倉庫内物流業務において重要な役割を果たしています。しかし、ピッキング作業の効率を向上させるために、倉庫内のレイアウト見直しや人員配置の変更を行っても思ったような効果を得られない場合があります。そこで、注目されている解決策としてピッキング作業のプロセス見直しやピッキング作業の自動化が挙げられます。この記事では、ピッキング作業の重要性と役割、ピッキングミスが起こる原因を取り上げ、効率的なピッキング作業を実現するための手法について解説します。
ピッキング作業とは?倉庫管理における重要性と役割
ピッキング作業は物流センターや倉庫で行われる作業の一つであり、出荷指示があった商品を棚から集める作業です。正確なピッキング作業を行うことで在庫管理の精度が向上し、在庫の過剰や不足を最小限にできます。これにより、コスト削減や生産性の向上が実現されるなど様々なメリットがあります。
ピッキング作業の労力と重要性
ピッキング作業は、物流業務の中で最も重要視される作業です。ピッキングミスをすると顧客の信頼を失い、ペナルティーを課せられる場合もあります。ピッキング作業は、単調な作業であり多くの労力が必要です。そのため、効率的で正確な作業が求められます。
正確なピッキング作業で効率化
ピッキング作業を正確かつ効率的に行うことは、ピッキングミスの軽減や作業時間の短縮につながります。さらに顧客への正確かつ計画通りの出荷が可能となり、顧客満足度が向上します。運用マニュアルの整備など、ピッキング作業を効率化できるように工夫しましょう。
ピッキングプロセスの基本ステップと最適化策
ピッキング作業のみを効率化しても生産性向上には限界があります。そのため、ピッキング作業の前後の工程も含めたピッキングプロセスの見直しが必要となります。効率的な倉庫管理を実現するためには、一般的なピッキングプロセスと最適化策を知りましょう。
一般的なピッキングプロセス
一般的なピッキングプロセスは、受注→在庫引当て→ピッキング作業→検品作業→梱包→出荷という構成になります。これらの手順は、正確な出荷を実現するために重要な役割を果たします。
ただし、商品特性や倉庫レイアウト、リードタイムによって最適なピッキングプロセスは異なります。倉庫の責任者は自社の倉庫に最適なピッキングプロセスを選択する必要があります。
ピッキングプロセスの最適化策
ピッキングプロセスを最適化することにより、効率的な倉庫管理を実現できます。自社の商品特性や倉庫レイアウト、リードタイム、物量波動に応じて、最適なピッキングプロセスを確立しましょう。 最適かつ効率的なピッキングプロセスの確立は、ピッキング作業の標準化と効率化につながります。基本ステップとフローを把握し、自社倉庫に適した効果的な最適化策を導入しましょう。
ピッキングエラーの原因とその影響について
ピッキングミスが発生してしまうと自社に損失を被るだけでなく、顧客の信頼も損なわれます。今回は、ピッキングミスがもたらす多くの損失や問題点を解説します。
ピッキングミスの主な原因
ピッキングミスの主な要因は、商品違い(ロケーション間違い)、入数違い、荷合せミス、棚入れ間違いです。
ピッキングミスが発生した場合は、その原因を徹底的に追及しましょう。ミスが発生した理由を作業者や商品のせいにするのではなく、ミスを犯さない仕組みを作り上げることが重要です。
ピッキングミスは多くの損失の影響をもたらす
ピッキングミスが発生すると、損失を被るだけでなく、対応にも時間と労力がかかり顧客の信頼が損なわれてしまいます。また在庫数の違いによる補填や追加の経費などの経営的なマイナスが発生していまいます。 ピッキングミスの原因とその影響を正確に把握し、これらの対策を取ることで、顧客満足度の向上や会社の経費削減につながります。
ピッキング作業の最適化戦略、効率と精度を向上させる手法とテクニック
従来のピッキング作業は、ピッキングリストやスキャン検品など、限られた手法に依存していました。しかし、近年では様々なシステムの開発や自動化システムが導入されています。
また、ピッキング作業の動線を最適化することで、作業時間や移動距離が短縮され作業効率向上につながります。
ピッキング作業を効率化する手法
近年、ピッキング作業の効率化を目指してさまざまな手法が開発されています。
例えば、カートピッキングシステムやハンディターミナルシステムを使用して、ピッキングと同時に検品を行う方法があります。これにより、作業員はピッキングと検品を別々の手順として行う必要がなくなり、作業効率が向上します。
また、音声認識技術を活用したヴォイスピッキングシステムも存在します。
これらの新たな手法は、ピッキング作業の効率性を向上させると同時に、作業員の負担軽減に貢献します。
ピッキング作業のルート最適化
ピッキング作業において、ルートの最適化は非常に重要です。なぜなら、ピッキング作業を効率化しても作業動線が長くなると移動時間が増えてしまい、時間をロスしてしまいます。
そのため、ピッキング作業のルートを最適化することが大切です。ルートを最適化するポイントは、出荷頻度の高い商品を取りやすい場所に配置し、取りにくい商品は遠くや上下に配置するなど、レイアウトを工夫することです。また、ピッキング作業の動線にショートカットを設けることも効果的です。
バーコードスキャニングで正確な在庫管理
正確な在庫管理を行うためには、ピッキング作業を正確に行うことが重要です。具体的な手法として、バーコードスキャニングやハンディターミナルを使用した方法があります。 バーコードやハンディターミナルを使用したピッキング作業のメリットとしては、商品の取り間違いを防ぎ、トレーサビリティを確保できる点が挙げられます。また、ピッキング作業中に検品を行うことで、検品作業の削減など、工数削減のメリットも得られます。
ピッキング作業を正確に行うためには、バーコードスキャニングやハンディターミナルを活用しましょう。
自動化技術の導入で精度向上
ピッキング作業においてピッキング精度を向上させる一つの手段として、自動化、機械化があります。
例えば、自動倉庫やロボットを使用してピッキング作業を行うことで、人的ミスを減らし、効率的かつ標準化されたピッキングが可能となります。また、出荷事前情報(ASNデータ)の活用やシミュレーションソフトの活用により、さらにピッキング能力を上げることも可能です。
これらの手法を組み合わせることで、ピッキング作業の効率化を実現できます。ただし、倉庫条件や出荷要件に応じて最適な手法を選択しましょう。ピッキング作業を最適化することで、ピッキング作業は効率化され、精度が向上します。
ピッキング作業における自動化、ロボティクスの活用
現在、日本国内では労働力が減少しており、その補填には外国人労働者や高齢者の活用が必要ですが、体力の問題やコミュニケーション上の課題が存在します。その結果、さまざまな業種で自動化の流れが進んでいます。物流現場の実情としては、ピッキング作業より搬送業務の自動化が進んでいます。
ピッキング作業における自動化
ピッキング作業において、ピッキングの自動化は、まだ進んでいないのが実情です。倉庫内で行われる作業の中で、ピッキング作業と仕分け作業が最も大きな割合を占めています。仕分け作業に関しては一部自動化が進んでいますが、ピッキング作業は商品を掴むという工程があるため、自動化が難しく、まだ普及しきれていないのが現状です。
近年注目されているグッズ・トゥー・パーソン(GTP)
グッズ・トゥー・パーソン(GTP)は現在注目されている取り組みであり、業務効率化や作業者の負担軽減を目指して開発された方式です。具体的には、物流倉庫内で作業者が動かずに商品が作業者の前まで運ばれ、モニターなどを通じて指示通りに取り出す方法です。これにより、物流倉庫内での作業者の移動を最小限に抑え、歩行距離をゼロにすることで作業効率を向上させます。
現在、日本国内では労働力の減少が進んでおり、倉庫内作業の自動化の流れが進んでいます。そのため、グッズ・トゥー・パーソン(GTP)の導入が広まっています。
ただし、グッズ・トゥー・パーソン(GTP)の導入にはいくつかの課題や障壁が存在します。たとえば、導入には一定の費用がかかるため、投資対効果の検討が必要です。また、既存の倉庫や作業環境に合わせてシステムを設計・構築する必要があり、変更や改良には時間とリソースが必要です。さらに、自動化に伴う技術やセンサーの導入、そして維持管理なども重要な課題となります。
自社でグッズ・トゥー・パーソン(GTP)を導入するかどうか判断に迷った場合は、専門家に相談することをおすすめします。
まとめ
今後もピッキング作業の自動化は進んでいくと思われますが、完全な自動化にはまだ課題が残されています。グッズ・トゥー・パーソン(GTP)は、既存の作業者と自動化システムの組み合わせによる効率化の手法として、今後ますます注目されるでしょう。また、技術の進歩や環境の変化に合わせて、さまざまな改善や新たな取り組みが行われます。ここで大切なのは、作業者と自動化システムのバランスや調和を考えながら、持続的な改善を進めていく観点です。物流倉庫におけるピッキング作業にお悩みの企業の方は、お気軽にお問い合わせください。