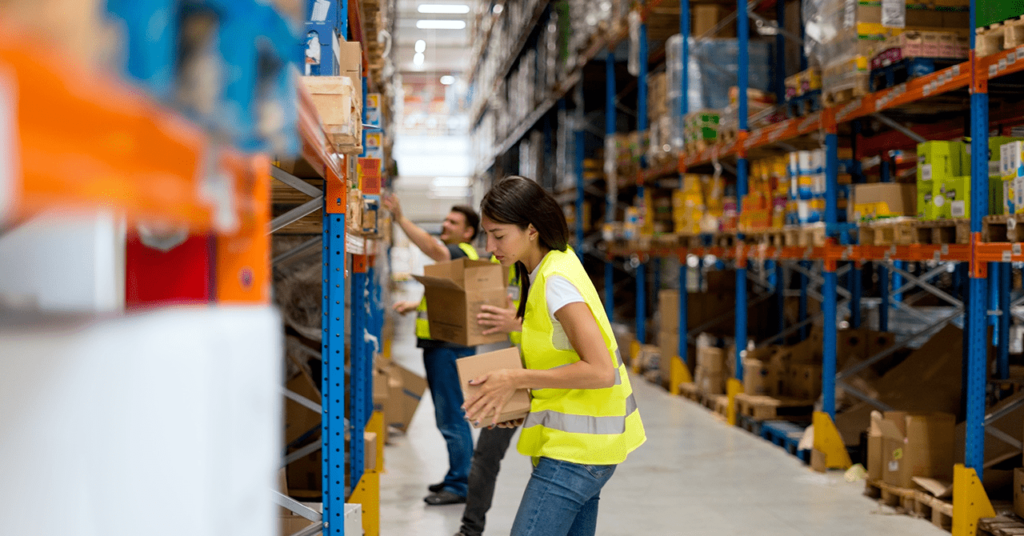
倉庫レイアウトは、倉庫内業務の作業効率に大きく影響を与えます。そこで、この記事では、倉庫レイアウトの問題点とそれを解決するためのポイントについて詳しく解説していきます。
倉庫レイアウトや運用方法が原因で発生する問題点
倉庫のレイアウトに起因する問題は、倉庫全体の業務に影響を及ぼす可能性があります。
ここでは、どのような問題が発生する可能性があるか解説します。
ピッカーの混雑
倉庫内でピッキング作業が行われている際、ピッカー同士が混雑してピッキング作業が滞留してしまうことがあります。
この問題はピッカーの作業効率を低下させ、手待ち時間を増やす原因となります。また、混雑状態では作業者のストレスも増え、やる気の低下やピッキングミス発生のリスクが高まります。
保管スペース不足
倉庫内の保管スペースが不足している場合、商品がラックに収まりきれずに、通路に商品を置いたり、作業スペースに商品を置いたりしている光景を見ます。
これに伴い、ピッキング時に通路に置かれている商品が邪魔だったり、棚札が見えなかったりしてピッキング作業効率が落ちてしまいます。また、先入れ先出しができなくなったり、棚卸しに時間を要したりして、在庫誤差にも繋がってしまいます。
問題点の解決方法
上記の問題を解決するために、倉庫レイアウトの最適化に取りくみましょう。これらの問題を解決することで、作業効率と生産性を向上させることに繋がります。解決方法は以下の通りです。
通路幅の見直し
ピッカーの渋滞を解消する有効的な手段として、
- 適切な通路幅にする
- 商品配置を変える
の2点があります。通路幅は商品の大きさや形状でも決まるものですが、出荷頻度にも目を向けましょう。
出荷頻度の低い商品に対して広い通路は必要ありません。逆に出荷頻度の高い商品はピッカーがアクセスする回数も多くなりますので、通路幅を広くして渋滞を避けなければなりません。
この出荷頻度により通路幅を調整するということは、出荷頻度を考慮した商品配置を行っている、ということが条件になります。
また、完全に出荷頻度順に商品配置すると、高頻度品が集まった位置でピッカーの渋滞が発生しますので、最も出荷頻度の高い商品はある程度、分散配置する必要もあります。
保管スペース不足の解決策
保管スペース不足の解決策は、
- スペースを生み出す
- 上部空間を利用する
- 空いた空間をつくらない
ことです。
「スペースを生み出す」とは、先ほどあげました通路幅の調整もその一つです。また、「上部空間を利用する」ということもスペースを生み出すことになります。
「空いた空間をつくらない」とは、ラックの商品収納率を高めるということです。商品が収まりきれないラックもあれば、空間だらけのラックがあったりします。
適切なラック種類や棚板段数、棚板高さの調整ができていればラック内の空いた空間を削減することができます。
これらの解決策についてはミスター物流の「保管効率アップ」のページに紹介しています。ご参考ください。
まとめ
倉庫レイアウトの最適化は、保管効率や作業効率を向上させるために非常に重要です。また、問題点を洗い出し、それに対する解決策を考えましょう。倉庫レイアウトを変更する際には、ぜひプロのアドバイスを受けることをおすすめします。
ミスター物流では、さまざまな業種におけるレイアウト設計の経験とノウハウを活かし、お客様の課題やニーズをヒアリングの上、最適なレイアウトをご提案いたします。