ピッキング
ハンディターミナル画面にピッキング指示を表示してピッキングにスキャン検品をして、ピッキング後には検品を行わないというのが主流になってます。
ピッキング指示&スキャン検品フロー
出荷指示データに基づき無線ハンディターミナルを使ってピッキングを行う場合の一般的な運用フロー図です。
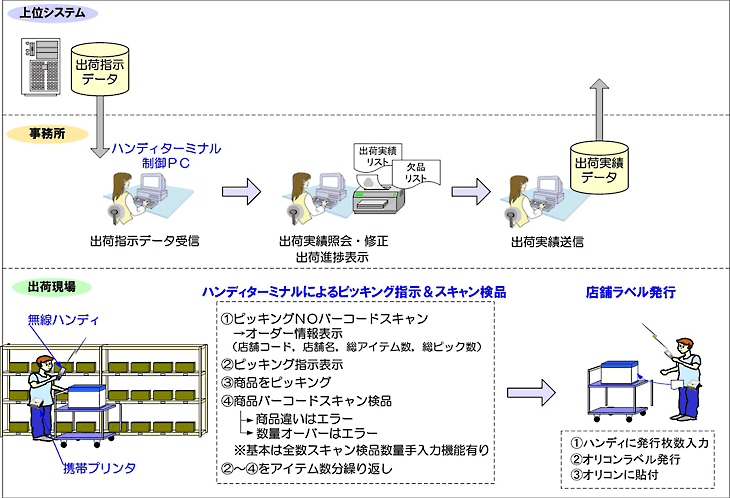
導入メリット
- ピッキング時に商品バーコードをハンディターミナルでスキャン検品しますので、商品知識の無い人でも、商品違いミス無くピッキングできます。
- 現場でのピッキング実績がPC(事務所側)にリアルタイムで送信されるので進捗管理ができます。
- ペーパーレスのピッキングが可能です(ピッキングリスト無しでもピッキング可能)。
- ハンディターミナルからのデータで作業者別生産性データを管理することができます。
ハンディターミナルでのピッキングシステムを導入する際の重要ポイントは、いかに生産性の高いピッキングができるかです。
ポイント
下記に生産性を上げるため、検討されるポイントをあげましたので参考にしてください。
- エリア分割してピッキングする
倉庫スペースが広くなると、全ロケーションを一巡してピッキングするよりも、エリア分割されたロケーション範囲をピッキングして、各エリアの荷合わせをした方が効率よくピッキングできます。 - 1つの出荷先の物量が多い場合、分割してピッキングする
新店向けのピッキングなど、ピッキング中に台車等に乗り切れなくなり、満杯になったコンテナ等をどこかに逃がさなければいけなくなります。出荷物量や容積計算で1件の出荷指示データを分割してピッキングするとこのようなことがなくなります。 - 1つの出荷先当たりの出荷行数が少ない場合、複数出荷先をまとめてピッキングする
通販の物流センターでよくありますが、在庫スペースが広くて1出荷先当たりの出荷行数が少ないと、歩行している時間の割合が多くなり効率的なピッキングができません。複数件まとめてピッキングすると効率よくなります。但し、ピッキングした商品と出荷先を間違えないような仕組みが必要です。 - ハンディターミナルで生産性目標値などをアナウンスする
1件のピッキング終了後にハンディ画面でピッキング時間や生産性結果などをアナウンスすると、ピッカーさんの生産性に対しての意識が向上します。