新センター計画担当者様へ
一般の企業において新センター計画が持ち上がり、その担当者に任命された人は、
「どういう手順で進めるべきなのか?」「どのようなことをすべきなのか?」
で悩むことが多いと思います。それは物流部責任者でも日常は自社物流業務の管理がメインであり、新センター計画のようなプロジェクトそのものが滅多に無いからです。新センターを頻繁に立ち上げている企業はその専門部署が有り、手順化、パターン化されてますが、一般の企業においてはPJメンバー全てが初体験というのも珍しくないはずです。
ここでは、そのような新センター計画担当者様向けに、「何をすればいいのか」を時系列でまとめてみました。当然、新センター計画の様々な条件により該当するものしないものありますが、何かの参考にして頂ければと思います。
縦軸でスケジュール感を表現してますが、これはセンター規模、新築か賃貸か、用地確保時の法的な対応などにより大きく変わりますので、あくまでも参考としてください。
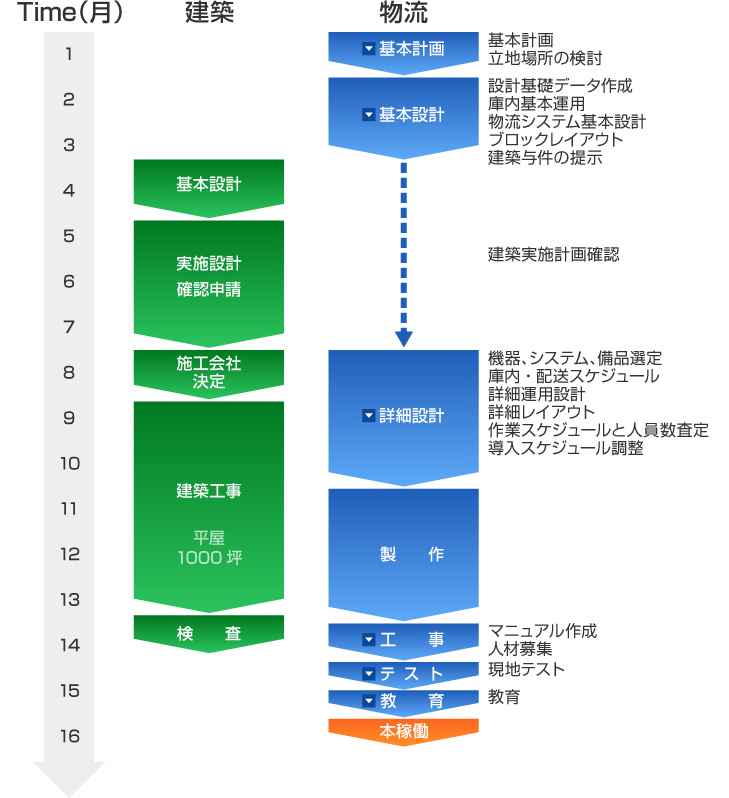
基本計画
このステップではセンター設立するためのコンセプトと基本的な設計与件を決めます。またPJメンバーを結成します
※PJ:プロジェクト
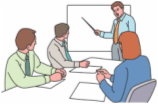
- コンセプトとセンター機能
新センターを設立する目的と主機能を明確にします。これは新センター計画が上がった時点で必然的に存在するわけですが、現状センターとの相違点、出荷精度などの目標値も含めて明確にします。これをPJメンバーの共通認識とすることが重要です。 - センターキャパ
出荷先件数、出荷物量、在庫物量などのセンターキャパを設定します。オーバーした場合は外部倉庫を借りるなどの対応策も決めておきます。 - 目標値や顧客サービスの設定
精度や顧客サービス、リードタイム短縮などの目標値を設定します。自社のみの都合で設定するのではなく、業界の方向性や他社との競争力を踏まえて設定します。 - PJメンバー選定
物流、情報、営業など必要部署からメンバーを選出します。各部署の責任者と実務者を選定して、PJをマネージメントできるリーダーを選出します。PJの責任者としては役員クラスになってもらうべきです。
立地場所の検討
下記の条件からセンター立地としてふさわしい地域を絞り込みます。絞り込んだ地域の土地や賃貸倉庫の調査を行います。
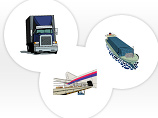
- 配送先条件
配送先マッピング図や配送時間指定、便数などから地域を絞り込む。 - 仕入れ先条件
仕入先マッピング図やセンター入荷時間などから地域を絞り込む。 - 交通アクセス条件
高速道路I/C、港湾、貨物駅、空港などの交通アクセス拠点とセンターとの距離。 - 用地条件
・賃貸倉庫を借りる場合、許容範囲内賃貸コストの地域。
・用地取得する場合、地価許容範囲内の地域。
・建築基準法や消防法、用途などから建設できる地域。 - センター配送地域条件
自社複数センターになる場合、各センター配送地域と配送先数を考慮した地域。 - 人員確保条件
センター内の作業者を確保しやすい地域。
設計基礎データ作成
ここではセンターを設計するための基礎データを確定させます。商品分類や荷姿(ケース、バラ、パレット等)、カテゴリー などで保管場所や運用が異なる場合はそれ毎に行ないます。曜日波動や月波動がある場合は、最小値、平均値、最大値の3つを確定させます。以下、参考例です。
- 商品別分析
アイテム数、アイテム毎在庫数、ABC分析(できるだけランク分けを多く)、ABCランク毎の回転日数など商品別の在庫数を確定させます。 - 出荷先分析
企業数、企業別出荷先数、物流センター納品、出荷先業態、出荷先別商品分類、企業別納品条件、出荷金額/年、出荷物量/年など出荷先に関する条件をまとめます。 - 1日当たりの処理量
1日当たりの処理量、物量などを確定して各作業場のスペース算出などの基礎データにします。
・入荷関連:アイテム数、物量、仕入先数、トラック数など
・出荷関連:アイテム数、行数、出荷物量、出荷先数、出荷什器数(カゴ車など)など - 1日当たり1出荷先当たりの処理量
出荷に関する作業ボリューム算出の基礎データになります。また出荷先数増加時のセンターキャパ設定にも活用できます。
・出荷関連:アイテム数、行数、出荷物量、出荷什器数(カゴ車など)など
庫内基本運用
センター内の各作業工程についての運用方法を確定します。この時、出荷先毎の納品条件や精度目標、庫内・配送スケジュールを考慮した設計が必要です。
- 入荷
- 入庫(棚入れ)
- 物流加工
- 在庫管理方法
- ロケーション管理方法
- ピッキング
- 検品
- 仕分け
- 荷合せ
- 積込み
これらをフロー図として作成します。設計基礎データから各運用での物量やアイテム数などの処理量を記入します。このフロー図を作成して今後の会議に活用しますが、変更があった場合はこのフロー図も修正して確認を行います。
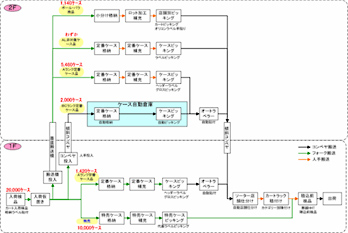
物流システム基本設計
- 現状システム活用
物流システムについては自社現状保有システム(基幹システムやWMS)を活用できるかを検討します。 活用できるのであれば、それをベースにしてシステム運用を決めていきます。また、現状システムからのカスタマイス内容をまとめておきます。 - 単体物流システム導入
デジタルピッキングシステムやソーターなどの単体物流システムを導入する場合は、現状システムとの機能切分けやインターフェイスするデータの概要をまとめます。 - WMS導入
WMS(倉庫管理システム)を新たに導入する場合は、仕様打合せ、設計、開発、導入までの期間がかかります。今後のPJでWMS分科会を設けるなどして、仕様打合せをしていく必要があります。
ブロックレイアウト
- 必要スペース算出
センター内で必要な在庫スペースや作業スペースの算出を行います。入荷荷捌き、在庫、各作業、仕分け、出荷待機 などのスペースがあります。在庫スペースは商品分類や荷姿毎に算出します。設計基礎データと庫内基本運用から各スペースを算出しますが、現状センターでの基礎数値が最も参考になると思います。 - 入出荷バース数
入荷バース数とトラックサイズ、出荷バース数とトラックサイズを決めます。これは配送スケジュールにも絡んできます。 - 大型マテハン機器
自動倉庫やソーター(自動仕分け機)などは機器そのものの設置スペースをとりますので、設置スペースや搬送、作業スペースを算出しておきます。 - ブロックレイアウト(ゾーニング)図作成
これを基にセンター内のブロックレイアウト図(ゾーニング)を2~3パターン作成します。このブロックレイアウト図が新センター像ということになります。
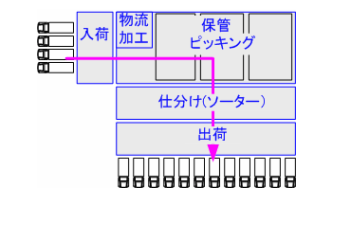
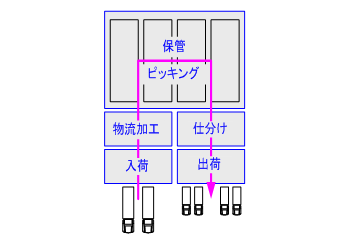
建築与件の提示と建築実施計画書確認
建築基本設計は建築設計会社が行いますので、新センター計画担当者としては、導入する物流機器や物流業務を考慮して、建築設計会社に物流に関する建築与件を事前に提示しておく必要があります。以下は、建築与件としての参考項目例です。
- 現状センターと新センターの比較、相違点
- 多層階センターの場合、各フロアの用途
- 柱スパン
- 庇の長さ・高さ
- 入出荷ホーム高さ
- 床仕上げ
- 換気、排気
- 防火区画を超える大型物流機器
- 休憩所スペース
- 階高と梁下有効高さ
- 高床式か低床式
- 床荷重
- 入出荷バース数とトラックサイズ
- 入出荷バースシャッター
- 照明
- 上下搬送、横搬送の開口、壁貫通
- 駐車場車両台数
建築設計会社からの建築実施計画書が出来上がったら、上記の内容に大きなずれが無いかを確認します。
建築サイドの理由から仕方ないものもありますので、この時点でしっかり建築設計会社と協議する必要あります。
機器・システム・備品選定
保管設備関連、搬送機器関連、ピッキング機器関連、仕分け機関連、物流備品など様々な機器があります。ミスター物流内の「システム」、「物流機器」のコーナーでは、機器やシステム毎の特徴やメリット、導入ポイントなどをまとめてありますのでそちらでご確認ください。
庫内・配送スケジュール
庫内スケジュール作成する場合、最も優先されるのは、受注締め時間とトラック出発時間です。これを実現できる庫内・配送スケジュールを組まなければなりません。
- 入荷と出荷
入荷に関してはメーカー工場からの出荷時間もありますが、一般的に入荷時間帯と出荷時間帯をわけることができれば、それがベターです。スペースや人員の有効活用できます。 - 人件費
作業時間帯により庫内作業者の採用しやすさや人件費がかわりますので、これも考慮しなければなりません。 - 全体最適化
物流効率アップ、全体最適化のために入荷時間、出荷時間についての調整は社内他部署や他社に積極的に提案すべきです。
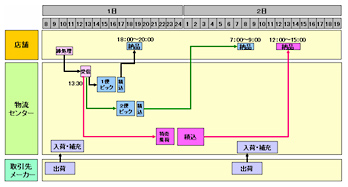
詳細運用設計
基本運用に添って現場運用、システム運用の詳細設計を行います。まず、ピッキングなどの1つの作業工程を細分化して、その細分化された作業内容を決定します。この時、重要なのがイレギュラー対応を徹底的に洗い出し、その対応方法を決定することです。
これが不十分ですと、テスト時に判明して急なシステム変更やハード改造をやらざるを得ないことになります。テスト時に判明しないと本稼働後のトラブル要因となります。
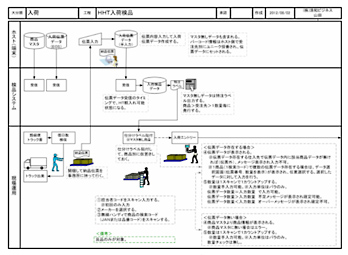
詳細レイアウト
- ブロックレイアウト
建築図面が完成したら、その図面(躯体図)に物流機器を落とし込みます。まず事前に描いたブロックレイアウトをラフに落とし込んで、センター内の流れ(入荷~在庫~出荷)を描きます。 - 物流機器の落込み
ラックやコンベヤなどの物流機器を躯体図に落とし込みます。通路幅や各作業場スペース、作業動線、作業効率、搬送能力、機器制御など物流機器に関しての知識と運用設計力が必要です。
この作業においてはCAD図面作成や細かい物流機器のサイズ、処理能力を考慮して設計する必要ありますので、設計与件を提示して、設計会社などに依頼すべきです。ミスター物流にご依頼ください。
作業スケジュールと人員数査定
各作業工程ごとの時間帯と作業者数を明記したタイムスケジュール表を作成します。フォーマットは様々ですが、重要なのは、「どのエリアで」「誰が(社員やパート)」「何人」「どういう作業を」「何時から何時まで」が表現できていることです。この表により時間帯毎の作業者数が見えてきます。
どの作業に何人必要かを設定するには生産性管理ができている必要あります。ミスター物流内の「生産性を上げたい」のページを参照ください。
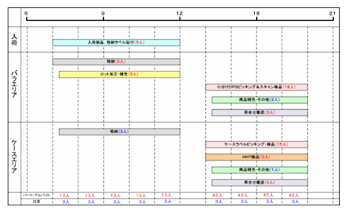
導入スケジュール調整
建築設計会社からの建築スケジュールをベースにして、物流機器メーカー、業者、に導入スケジュール表作成を依頼します。
建築側引き渡し後からの物流機器搬入がベストですが、規模の大きいセンターになると建築工事と物流機器工事が同時進行します。建築設計会社、各物流機器メーカーと搬入、工事、テストまで含め順調に導入作業が流れるようにスケジュール調整を行います。
物流機器メーカー数が多いとこのスケジュール調整は大変です。エンジニアリング会社に依頼するか、物流機器メーカー1社にその役割を依頼するかを検討した方がいいと思われます。
マニュアル作成(実運用ベース)
現場での総合テストや庫内作業者への教育に向けマニュアルを作成します。
物流機器やシステムの操作マニュアルはメーカーやシステム会社が作成しますが、それは担当する機器やPCの操作のみです。それらを基に実運用をベースとした作業マニュアルや操作マニュアルを作成します。
このマニュアルは現場や商品の写真を使うなどして見やすく理解しやすく作ります。また、注意点や禁止事項を盛り込みことも重要です。
人材募集
庫内作業者は極力、パートやアルバイトで構成できるようにした方がベターです。集まらなければ派遣会社に頼らざるを得ませんが、短期間で人がころころ変わるので、教育に手間がかかり、作業精度も大きく落ちてしまいます。
現地テスト
現地でテストを実施して、仕様書通りか、運用ベースで問題点が無いかを確認します。ここで修正必要な点が発生する場合ありますが、焦って修正依頼をするのではなく、PJメンバー内で今までの打合せの経緯など振り返り、総合的判断が必要です。
- 単体テスト
システム単体テスト、物流機器単体テストを行い、要件通りの機能が備わっているか、パフォーマンスは合格か、などの検証を行います。 - インターフェイステスト
システム~システム、システム~物流機器の通信が問題ないか、現場インフラ環境でのインターフェイステストを行います。 - 運用テスト
入荷やピッキングなどの各運用に対して、実運用を想定しての運用テストになります。事前に作成したマニュアルに従って行い、運用として問題ないかを確認します。 - 総合テスト
1日の庫内運用、システム運用のテストを行います。このテストで稼働を向かえてOKかの最終判断になります。
教育
- マニュアルでの教育
作成した実運用ベースのマニュアルで教育を行います。マニュアルを正として行いますが、見直した方がいい点などは、1日最後の反省会などで取り上げ、PJメンバー同意の上で見直しをかけます。 - 教育環境作り
実商品を使えない場合はサンプル商品などを作り、より実作業に近い教育環境を作りあげて実施します。 物流業務は机上だけの教育ではほとんど習得することはできません。 - 人員配置
できるだけ早く人の質、レベルを読み取り適材適所の人員配置を行います。 - 職場環境
パート・アルバイトから改善要望など積極的な意見が上がる環境作りを心がけます。